shell core sand preparation process
2022-10-13T10:10:24+00:00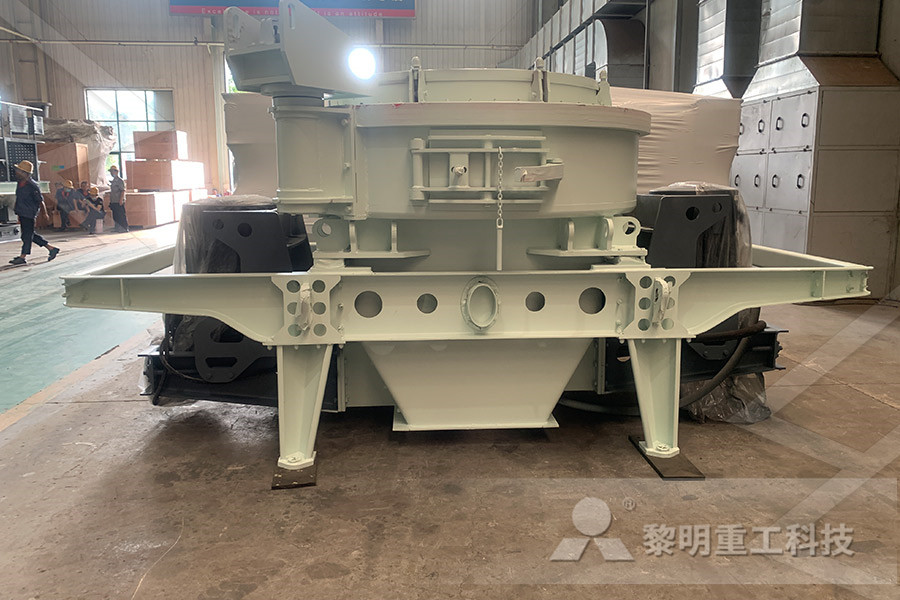
Sand Casting Shell Machine Shell Core Machine
Shell cores can be solid, smooth with high definition The shell process can also be used to create molds providing a casting with excellent finish and minimum cleaning room processing The shell core can be cured with either electrical heated platens or gas fired systems, and the uncured sand can be reused after collectionThe Shell Sand process or "Croning" process was invented by Dr Johannes Croning in Hamburg, Germany in 1944 This process is the oldest core and mold making technology that utilizes synthetic resins Although many additional sand core and molding making technologies have since been introduced, the Shell Sand process is still a very effective Resin Coated Sand HAInternationalMar 08, 2011 The core mix was then compacted in the core mould with a vent made by a wire through the middle to aid in the dispersion of the CO2 and gases during the metal pourCore sand casting experiment Part 1 YouTube
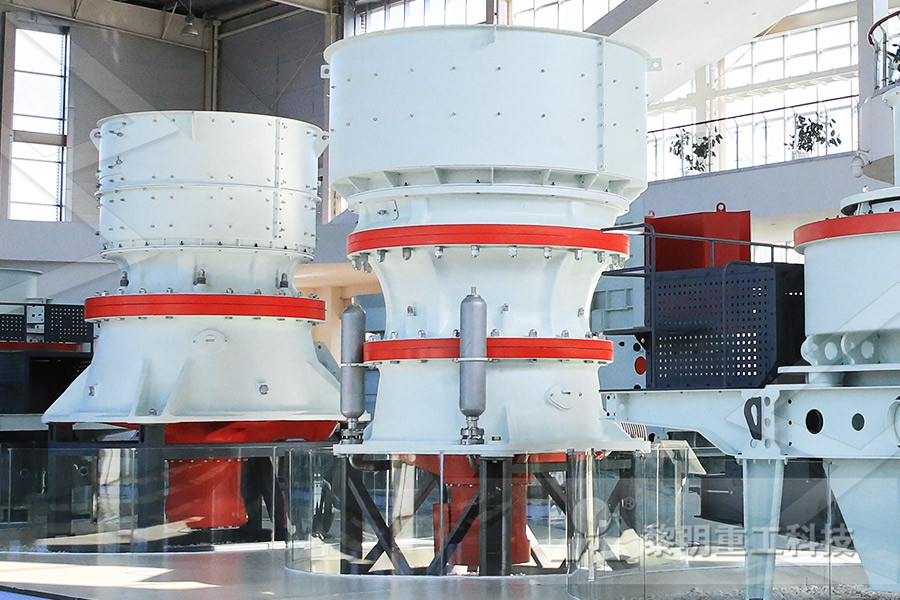
(PDF) A STUDY OF CORE AND ITS TYPES FOR CASTING PROCESS
A STUDY OF CORE AND ITS TYPES FOR CASTING PROCESS molding sand preparation, sand mixing, core Heated core box is employed for making shell cores from dry resin bonded mixturesApr 10, 2018 Kao Kuen Industrial Co, a professional manufacturer of core shooting machine and shell molding machines, has accumulated a solid knowledge and experience in making most effective, economic and Core Shooting Machine, Shell Molding Machine, Sand Core The Shell Process uses a blend of dry sand, with resin coating applied, blown into a metal “corebox” to form a sand core Core boxes are typically made of some type of metal, usually iron or aluminum The core box is heated by natural gas to temperatures of 450 to Shell Supreme Cores, Inc / Sand Cores / USA CAN
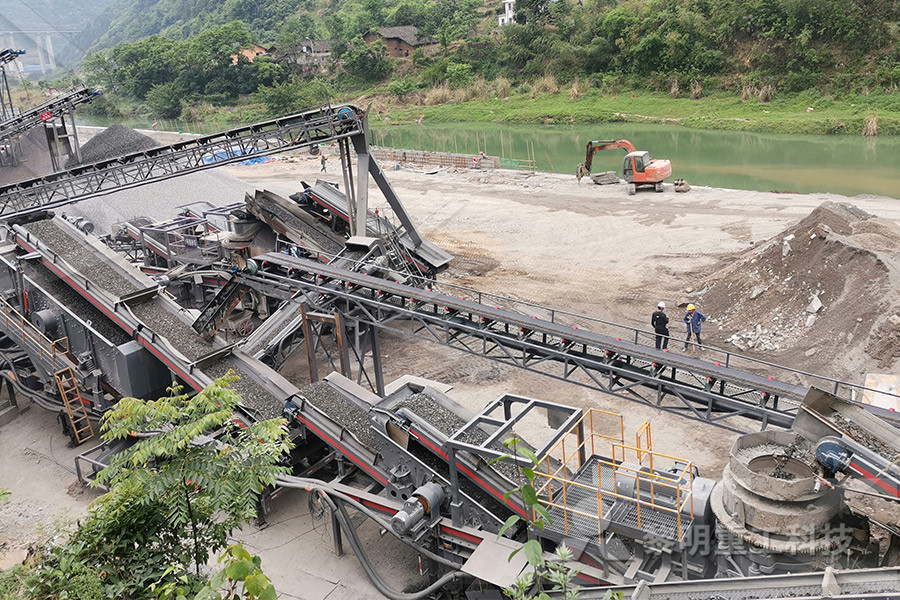
Core (manufacturing) Wikipedia
When the corebox is opened and the core removed, the uncured sand inside the core is dumped out to be reused This practice can also be observed in some coldbox coremaking practices, though cold box shellcore making is much less common In a similar vein, the coldbox process uses a binder that is hardened through the use of special gases Through our partnership with Savelli Srl and Küttner GmbH – EMI is now positioned to deliver complete green sand preparation and return systems to the North American market The Savelli greensand preparation systems offer innovative features that improve upon the traditional green sand molding process – highest quality castings – high Sand Preparation Systems Core ManufacturingCore Making Machines Shell Sand Preparation Equipments Automation of Existing Foundry Equipments It has given a foundry engineers an edge in the productivity of core making This process offers many advantages over the normal core shooters such as high productivity, energy saving, good dimensional accuracy, excellent break down properties Core Making Machines, Shell Moulding Machines, Automatic
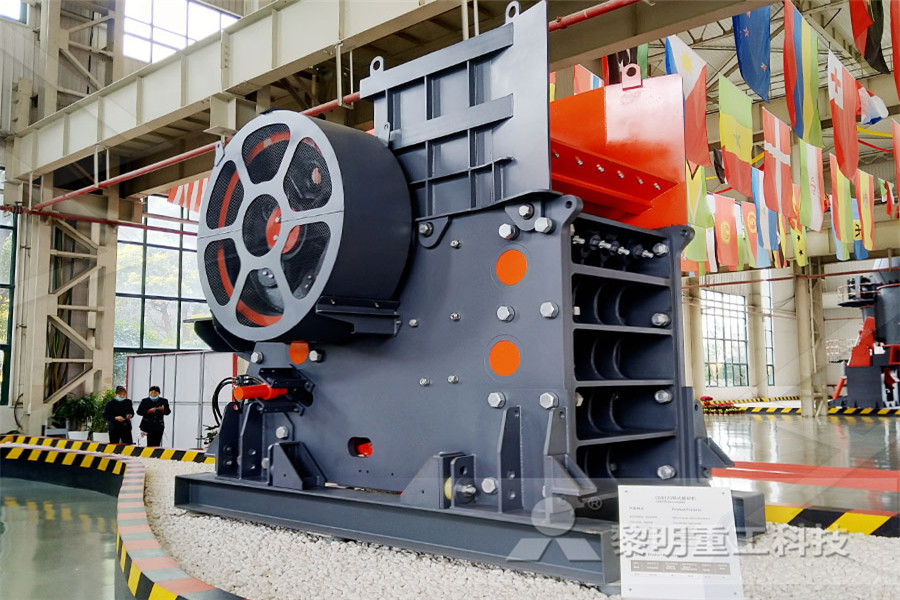
Core Making Machine, Core Making Machine Supplier and
These and other associated parameters are required for guaranteeing quality manufacturing in modern foundry operations Today, as complex designed core making systems need to deliver highest level performance as part of involved foundry process, it is also to be seen that automated processes are evolved for handling material handling operations so as to ensure best outputsShell Mold Casting Shell mold casting or shell molding is a metal casting process in manufacturing industry in which the mold is a thin hardened shell of sand and thermosetting resin binder, backed up by some other material Shell molding was developed as a manufacturing process during the mid20th century in GermanyShell Mold Casting Manufacturing ProcessShalco U180 Constructed of heavy iron castings and, like all Shalco Core Blowers, the U180 is manufactured with machine tool precision to provide sustained accuracy and long production life Its operation is fully automatic and allows the attendant to attend two or even three machines since it is only necessary for him to return to each Shalco U180 Shell Core Machine Alumco Foundry
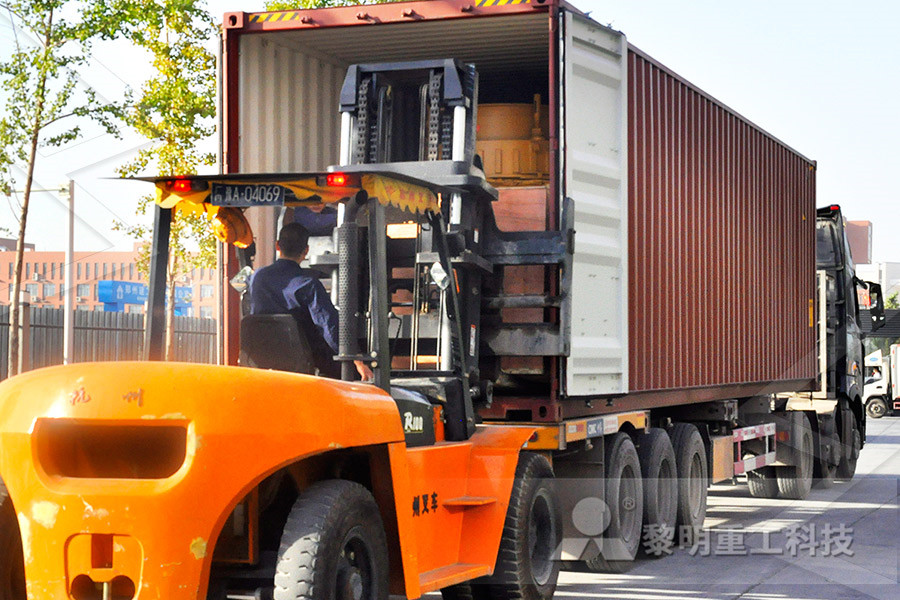
Sand Preparation Simpson Technologies
The cookie settings on this website are set to "allow cookies" to give you the best browsing experience possible If you continue to use this website without changing your cookie settings or you click "Accept" below then you are consenting to thisThe molders must also take great care to avoid unnecessary friction between the vanes and the core so the vanes are inserted snug to the core without rubbing loose any significant amount of core sandA loosefitting vane in the core introduces a level of variation in the process Core sand Article about core sand by The Free DictionaryThe next chapters provide the testing procedures and routine control of sand, silica, nonsiliceous materials, binders, and clay bond These topics are followed by discussions on sand preparation, shell mould, and other core materials, such as furanes This book describes some steel foundry processes, including heat extraction, casting, and hot Mould Core Material for the Steel Foundry ScienceDirect
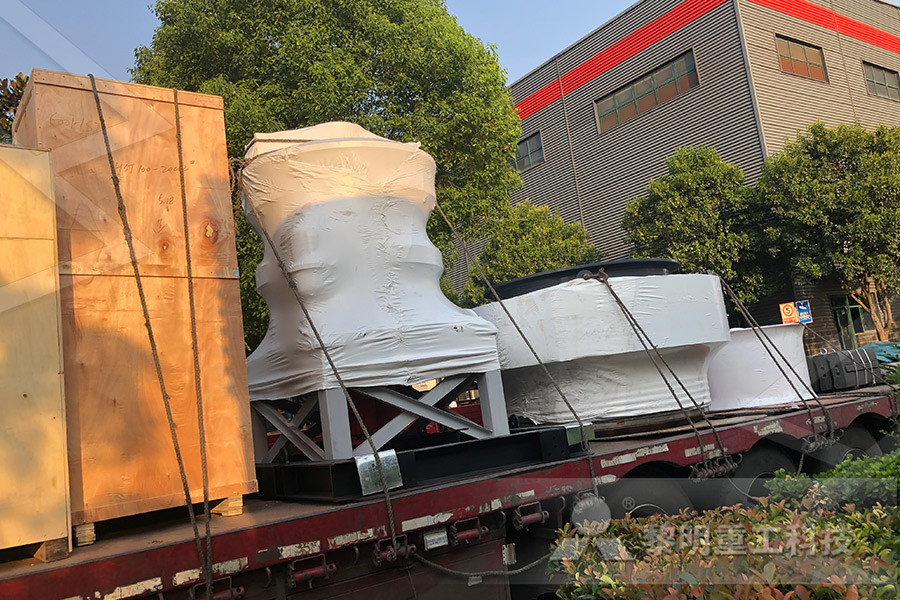
Primafond Foundry machines equipment production for cold
Sand preparation and distribution systems with batch mixers for any core production process; Core shooter machines for 5 to 150 litres cold box processes; Automatic gas generators for any kind of process; Core shooter machines for inorganic processes; Core shooter machines for shell moulding /croning; Special application machines on requestSand casting, the most widely used casting process, utilizes expendable sand molds to form complex metal parts that can be made of nearly any alloy Because the sand mold must be destroyed in order to remove the part, called the casting, sand casting typically has a low production rate The sand casting process involves the use of a furnace Sand Casting Process, Defects, DesignApr 13, 2020 Cores are used to produce caivities in the casting For Ex: Let us take an example of the engine cylinder block The cavity where the movement of pistons take place is hollowEngine block is manufactured by foundry industries Now the to keep thatWhat is core in foundry? Quora
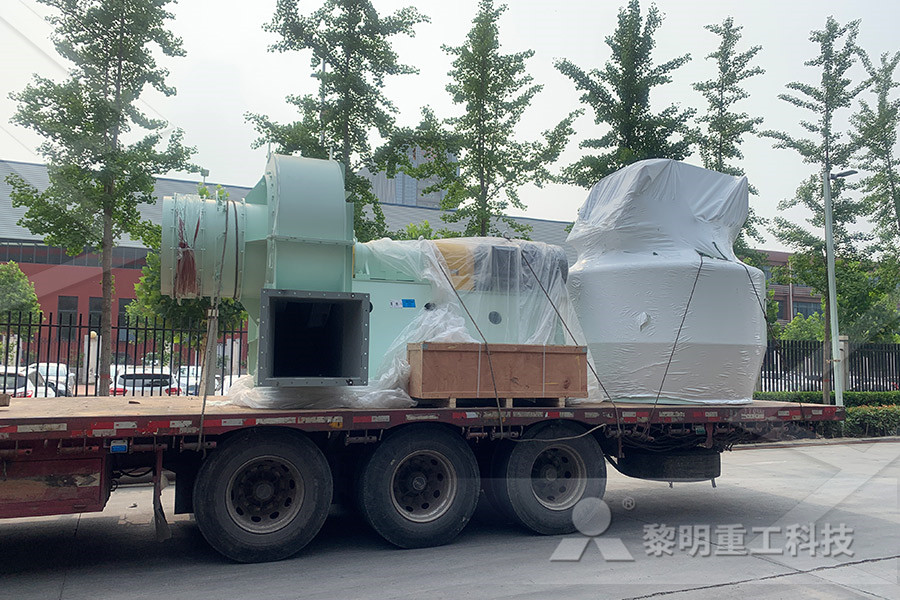
Study 34 Terms Ch 11 Manufacturing Flashcards Quizlet
Shell molding is best described by which one of the following: (a) casting operation in which the molten metal has been poured out after a thin shell has been solidified in the mold, (b) casting process in which the mold is a thin shell of sand bonded by a thermosetting resin, (c) sandcastingPreparation of montmorillonite modified phenolic resin for shell process By Xiong Jianmin, Li Yuancai and Wang Wenqing Abstract The development of montmorillonite modified phenolic resin under microwave irradiation heating was investigated The effect of montmorillonite content and stirring time on the structure and morphology of synthetic CORESand casting is a process that utilizes nonreusable sand molds to form metal castingsIt is a common production method for metal components of all sizes, from a few ounces to several tons Sand casting isn’t only versatile in the size of its products – it can also create exceptionally complex or detailed castings, and can be used to cast nearly any metal alloySand Casting Metal Casting Resources
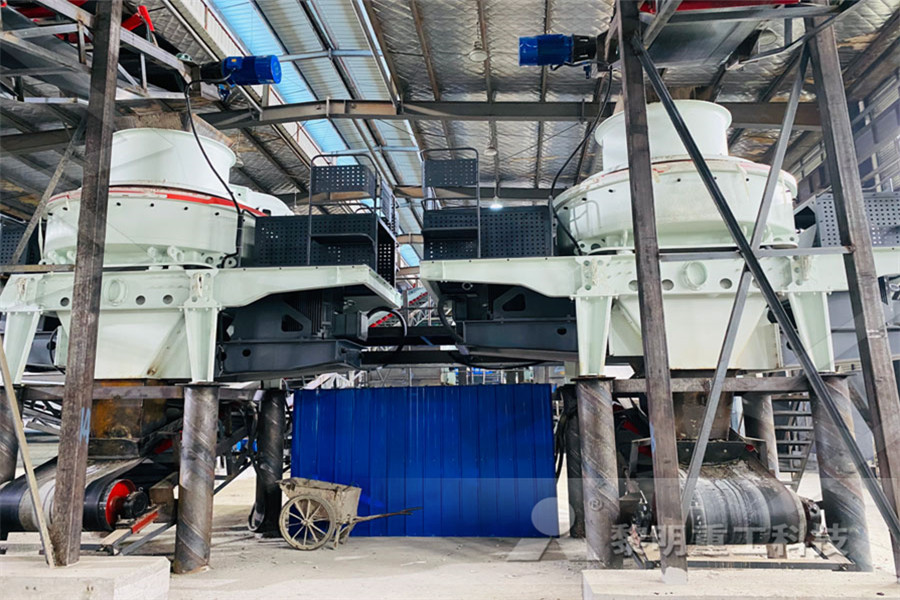
Molding presentation LinkedIn SlideShare
Feb 16, 2011 Pattern Preparation Pattern: Lower Half Core with structural reinforcement 10 Molding The elements of the foundry design are put in place: gates, funnel, molds, feeders; The box is filled with a mixture of sand and resinshell molds and sand molds both use sand as a mold medium, but in different ways sand molds create cavities with in the sand and pours the molten metal inside the cavity while shell molds create a pattern, places the patter in a box with sand /binder mix the sand/ binder is then placed on the to the pattern and creates a sand mold over the chapter 11 Flashcards QuizletAug 05, 2013 The only disadvantage seen is the process is slow Also the process requires heat curing so the rate of shell mold and core making is often limited by the rate of heat transfer through the resincoated sand Shell core making process allows sand to be precoated with a resin and then poured into a preheated boxShell Core Making system; an Efficient Core Manufacturing
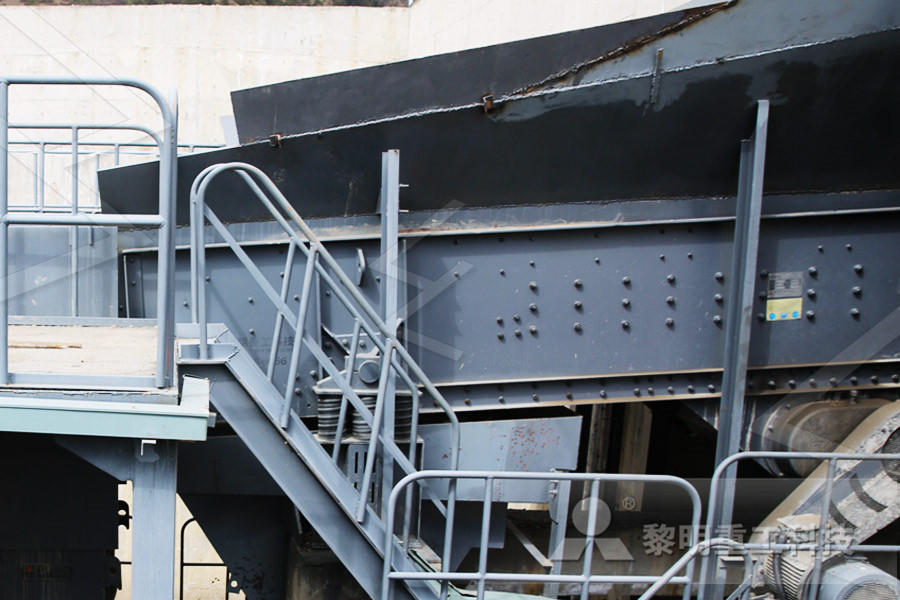
Sand Cores Wisconsin Foundry Sand Cores MidWest Core
Shell cores can be stored at high temperatures in humid conditions and have an indefinite shelf life Our core machines are capable of handling almost any size core box and we offer multiple blends of sand to manufacture cores to fit the unique needs of the foundry Warm Box Process In the Warm Box process the core box is warm when the core Shell Mold Casting Shell mold casting or shell molding is a metal casting process in manufacturing industry in which the mold is a thin hardened shell of sand and thermosetting resin binder, backed up by some other material Shell molding was developed as a manufacturing process during the mid20th century in GermanyShell Mold Casting Manufacturing ProcessShell molding casting also known as Resin coated sand casting, this process is precise than sand casting and cheaper than investment casting Makewell Inducto Cast Private Limited Odhav, Ahmedabad Plot No 471/510, Phase II, Road No 12/13 Kathwada, G I D C, Odhav, Ahmedabad , Dist Ahmedabad, GujaratShell Moulding Casting Shell Molding Casting
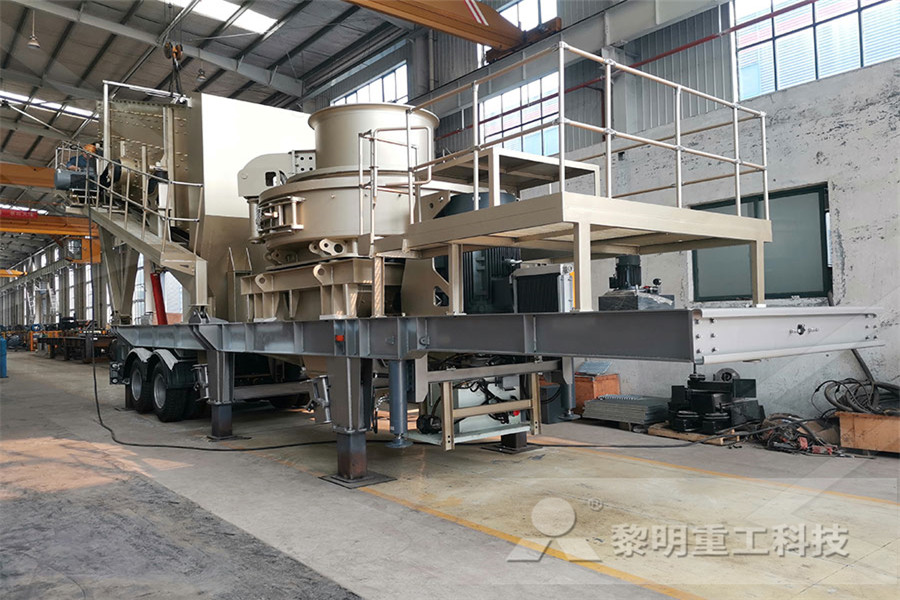
The Different Methods of Core Making Tinker Omega
Oct 04, 2013 Shell core making is a method where sand is precoated with resin and then poured into a preheated core box No catalyst is used in this process and instead heat is introduced in the surface of the box until it forms a thin, hard shell This allows the sand on the inside of the core to remain uncured and removed by pouring it out from the coreThese and other associated parameters are required for guaranteeing quality manufacturing in modern foundry operations Today, as complex designed core making systems need to deliver highest level performance as part of involved foundry process, it is also to be seen that automated processes are evolved for handling material handling operations so as to ensure best outputsCore Making Machine, Core Making Machine Supplier and Apr 13, 2020 Cores are used to produce caivities in the casting For Ex: Let us take an example of the engine cylinder block The cavity where the movement of pistons take place is hollowEngine block is manufactured by foundry industries Now the to keep thatWhat is core in foundry? Quora
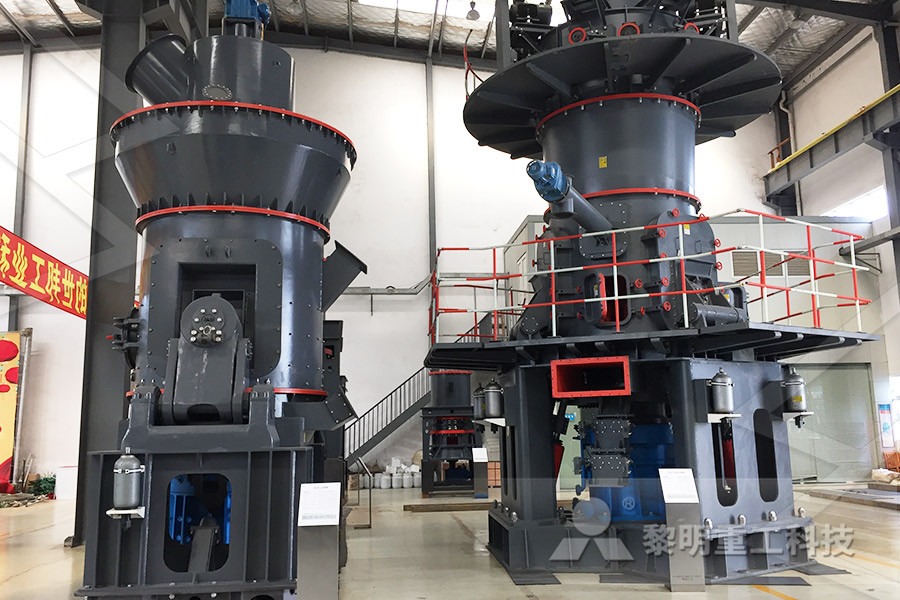
Materials Chapter 12 Review Questions Flashcards Quizlet
Start studying Materials Chapter 12 Review Questions Learn vocabulary, terms, and more with flashcards, games, and other study tools What material serves as the binder in the shellmolding process, and how is it cured? What is the sand binder in the coreoil process, and how is it cured?By continuously developing a full range of proven, integrated sand preparation and control technologies, Simpson Technologies can benefit any size or type of foundry by providing a complete solution from a single source that best: • provides consistently highquality sand preparation system performance with minimal process variationFOUNDRY SAND PREPARATION Simpson TechnologiesThis test will determine the percent of resin in the sand sample In order to keep quality at an exceptional level at the point of production we use first core quality checks, process sheets, a shell color chart and Baume check sheet First Core Quality Check – This is done by all of our supervisors and lead personnel When the first few QUALITY Supreme Cores, Inc / Sand Cores / USA CAN
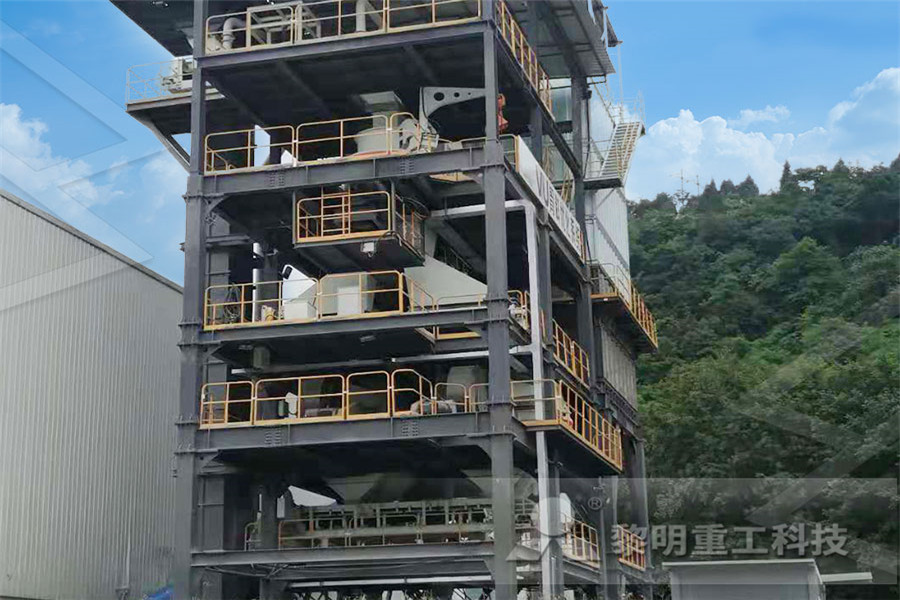
Sand Casting Hot Sheel and Core Molding Process
Dandong Foundry owned many sets of singlestation and doublestation coremaking machines We adopt advanced shell core tech besides hot box, especially for key parts It improves the smoothness and dimensional precision, reduces the machining, increases efficiency of labor, decreases material costSand casting, the most widely used casting process, utilizes expendable sand molds to form complex metal parts that can be made of nearly any alloy Because the sand mold must be destroyed in order to remove the part, called the casting, sand casting typically has a low production rate The sand casting process involves the use of a furnace Sand Casting Process, Defects, DesignShalco U180 Constructed of heavy iron castings and, like all Shalco Core Blowers, the U180 is manufactured with machine tool precision to provide sustained accuracy and long production life Its operation is fully automatic and allows the attendant to attend two or even three machines since it is only necessary for him to return to each Shalco U180 Shell Core Machine Alumco Foundry
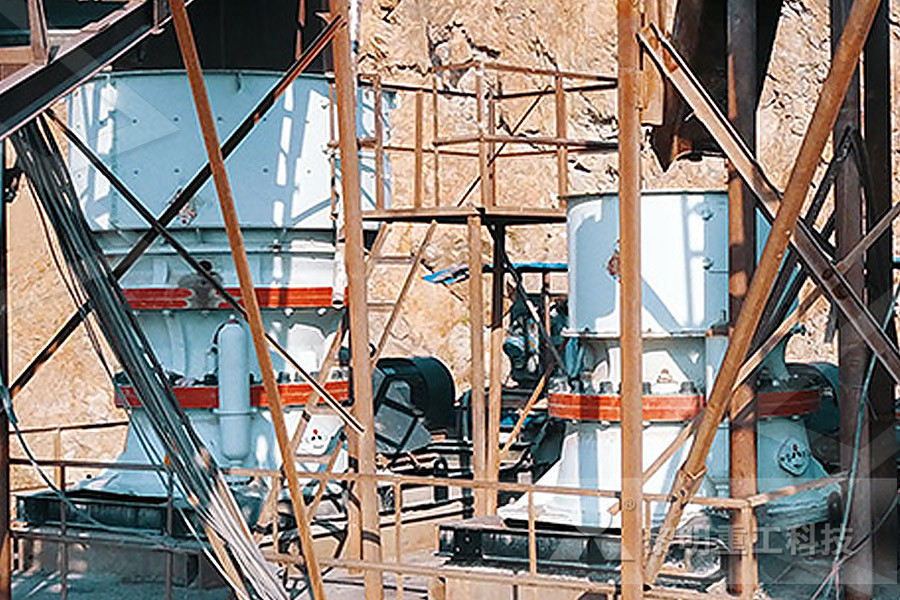
Study 34 Terms Ch 11 Manufacturing Flashcards Quizlet
Shell molding is best described by which one of the following: (a) casting operation in which the molten metal has been poured out after a thin shell has been solidified in the mold, (b) casting process in which the mold is a thin shell of sand bonded by a thermosetting resin, (c) sandcastingDandong Foundry owned many sets of singlestation and doublestation coremaking machines We adopt advanced shell core tech besides hot box, especially for key parts It improves the smoothness and dimensional precision, reduces the machining, increases efficiency of labor, decreases material costSand Casting Hot Sheel and Core Molding ProcessSand casting, the most widely used casting process, utilizes expendable sand molds to form complex metal parts that can be made of nearly any alloy Because the sand mold must be destroyed in order to remove the part, called the casting, sand casting typically has a low production rate The sand casting process involves the use of a furnace Sand Casting Process, Defects, Design
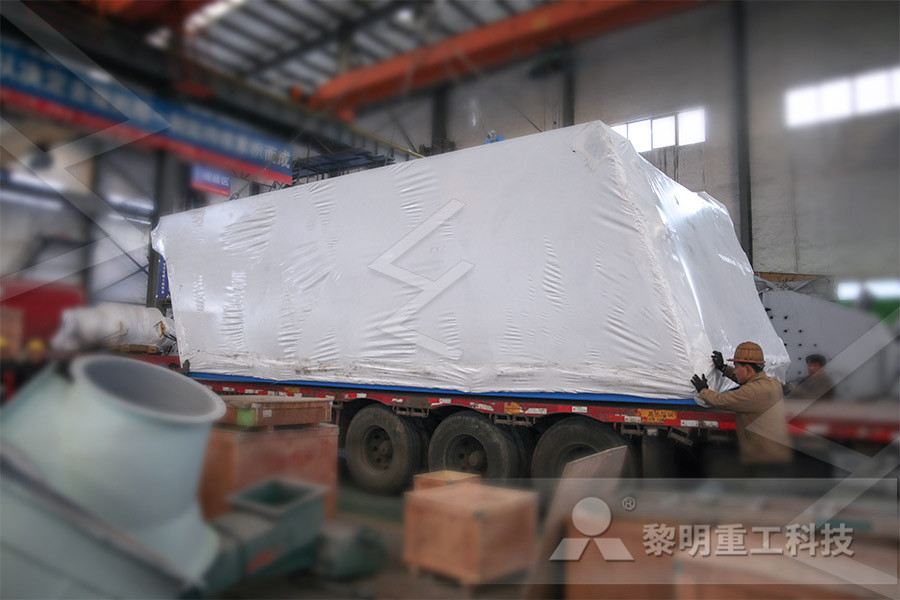
Shalco U180 Shell Core Machine Alumco Foundry
Shalco U180 Constructed of heavy iron castings and, like all Shalco Core Blowers, the U180 is manufactured with machine tool precision to provide sustained accuracy and long production life Its operation is fully automatic and allows the attendant to attend two or even three machines since it is only necessary for him to return to each Shell molding is best described by which one of the following: (a) casting operation in which the molten metal has been poured out after a thin shell has been solidified in the mold, (b) casting process in which the mold is a thin shell of sand bonded by a thermosetting resin, (c) sandcastingStudy 34 Terms Ch 11 Manufacturing Flashcards QuizletCores and Shell Core Making When implementing the SemiPermanent Mold Casting process there are two types of cores that can be included into a mold to create a desired design of a casting: Sand Cores and CastIn InsertsCores and Shell Core Making Ramsden Industries
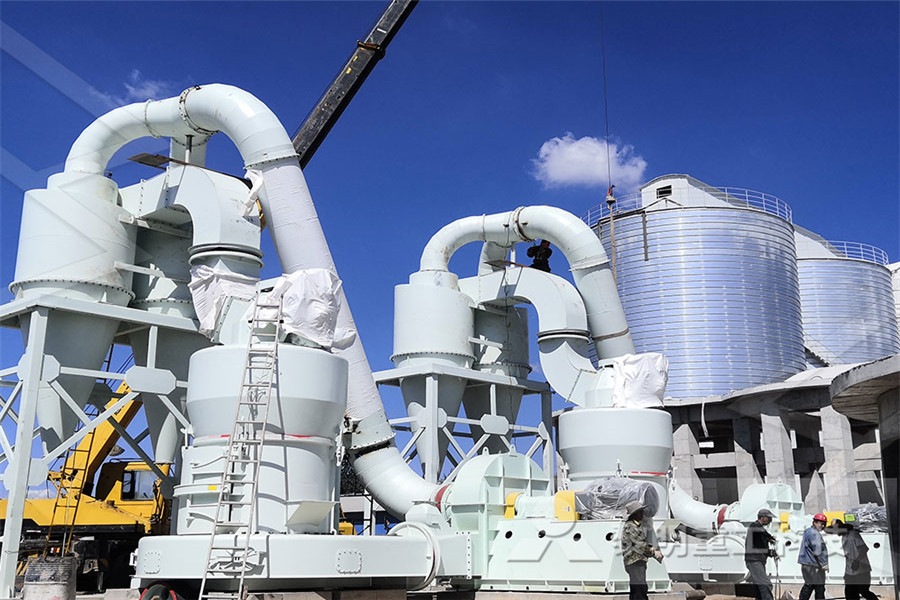
Foundry Supplies Equipment Midvale Industries
Midvale Industries is a proud Corporate Member of the following Associations: Midvale Freedom Products Midvale has developed a line of custom foundry products called Freedom Products which includes all of the products you need to create a perfect castingFor producing a casting of high precise dimensions, smooth surface, free of blow holes to avoid casting defects you must use shell molding process therefore Resin Coated Sand We manufacture all grades of resin coated sand for the preparation of shell cores and moulds either by conventional dump box method or by core shooterResin Coated Sand Resin Coated Sand Manufacturer Resin Semi Permanent Mold Aluminum Foundry Alcast's Low Pressure Semi Permanent Mold Aluminum Casting Process also uses the magic of ELECTROMAGNETICSIt is a refined process that has been practiced for over 30 years in our aluminum foundry!This type of casting incorporates a sand core in the design of the partSemi Permanent Mold Aluminum Casting in Aluminum Foundry
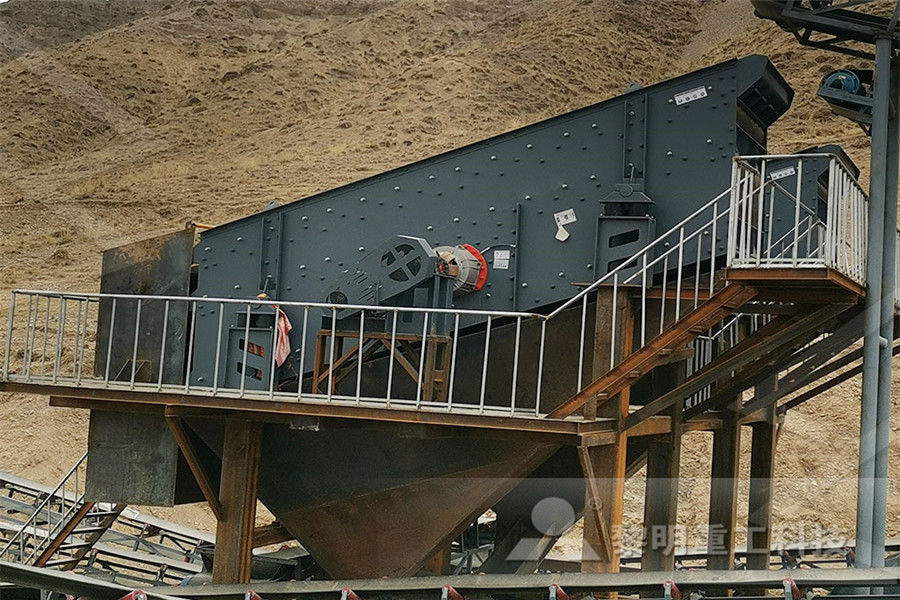
Aluminum and Brass Foundry Shell Cores NoBake Cores
Shell Cores the most efficient and economical way to use cores with sand casting molds Shell cores are long lasting and can be used for several months of production Longview Brass and Aluminum makes shell cores utilizing our five core machines and versatility is the key to our Core Room worksufficiently To further complicate the PUCB core making process, it is often the case that a venting scenario that will work well for the core shooting process may not be optimal for the subsequent curing process Other binder systems such as inorganic and resin coated shell sand require a homogenous tempering of the core box to ensureSimulation of the entire core production processThe shell process' chemistry is relatively simple: phenolic novolak resin and hexa are combined and coated on sand When the resincoated sand is exposed to a heated (450600F) corebox or pattern, the resin melts and bonds the sand to form a cured shell core or moldThe shell process: taking a new look Free Online Library

(PDF) Preparation of core–shell latex particles by
A series of core–shell polymeric particles with poly(nbutyl acrylatecomethacrylic acidcoethylene glycol dimethylacrylate) as core and poly(styrenecomethyl Sand casting is a process that utilizes nonreusable sand molds to form metal castingsIt is a common production method for metal components of all sizes, from a few ounces to several tons Sand casting isn’t only versatile in the size of its products – it can also create exceptionally complex or detailed castings, and can be used to cast nearly any metal alloySand Casting Metal Casting Resourcesthe humidity of the surrounding atmosphere The shell building process consists of one or two prime coats, four to five back up coats and a seal coat Then pattern is removed from the shell by melting wax or thermal decomposition of foam and shell is cleaned MetalCeramic Shell Interactions during Investment Casting