wet process of manufacturing of cement
2019-05-24T00:05:47+00:00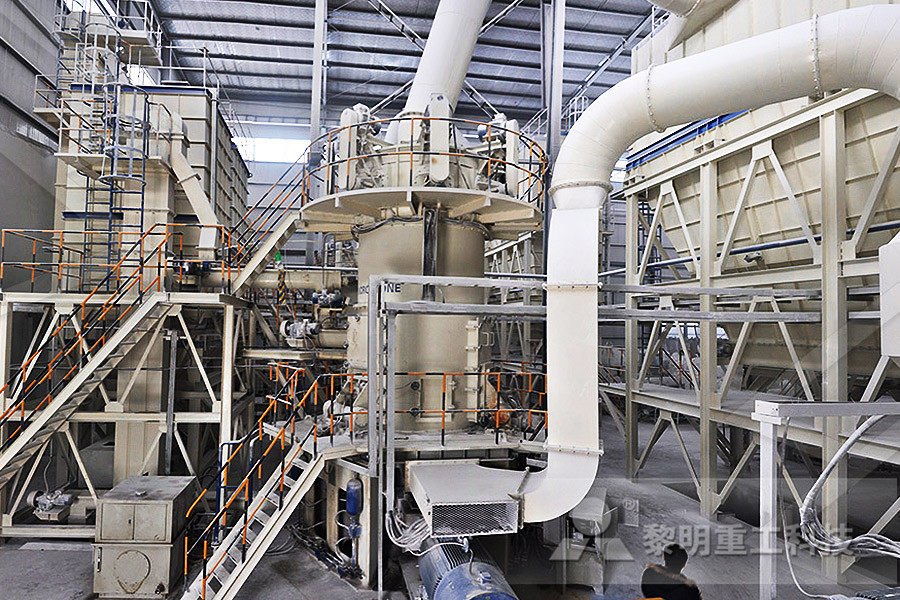
Wet Process for Manufacturing of Cement GharPedia
The kiln has to operate continuously in order to ensure a steady regime, and therefore uniformity of clinker The larger existing kiln in a wet process plant produces 3600 tonnes of clinker per day The manufacture of cement by wet process is energy intensive and thus uneconomical as compared to dry process and semi dry processThere are two different processes for manufacturing cement wet process minerals are wet ground (by adding water) to form a slurry and then dried, dry process minerals are dry ground to form a powderlike substance Both the processes are in use and have their own advantages and disadvantagesDifference Between Wet And Dry Process Of Cement The wet process of cement manufacturing involves adding water to finely crushed raw material, such as limestone, clay or iron ore, in a proportion of 35 to 50 percent water to 50 to 65 percent raw material to make a slurry that is fed into a cement kiln, whereas no water is added in the dry processWhat Are the Differences Between the Wet and Dry Processes
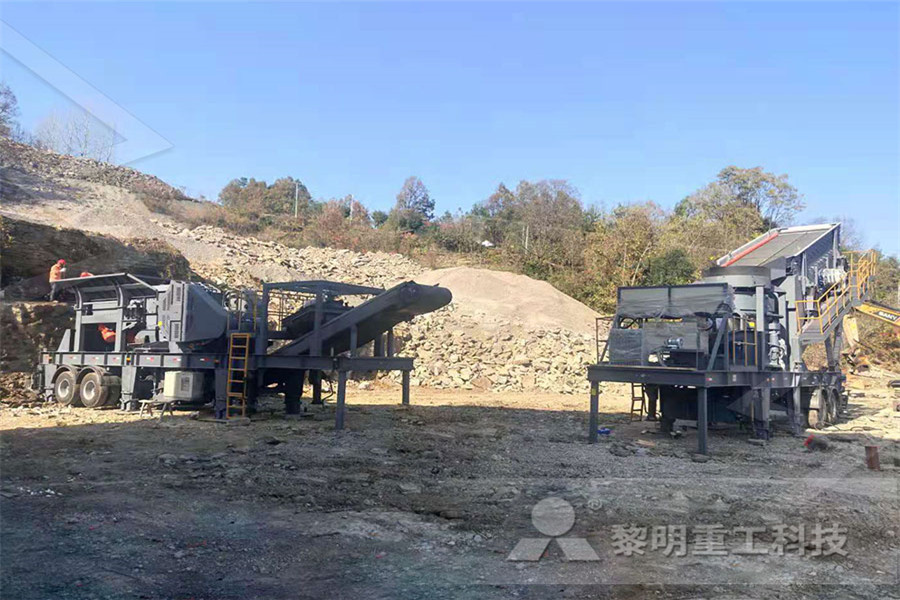
Wet process cement Britannica
Other articles where Wet process is discussed: cement: Manufacture of cement: manufacture are known as the wet, dry, and semidry processes and are so termed when the raw materials are ground wet and fed to the kiln as a slurry, ground dry and fed as a dry powder, or ground dry and then moistened to form nodules that are fed toMethods of Manufacturing Process of Cement At present Portland Cement is manufactured by two processes, Dry Process, and Wet Process The main difference between these two methods of manufacturing of cement is that in the dry process, calcareous and argillaceous raw materials are fed into the burning kilns in a perfectly dry stateCement Manufacturing Process: What is Cement made ofSep 24, 2018 Wet process 1 Mixing of Raw materials in wash mill with 35 to 50% water 2 Materials exiting the mill are called “slurry” and have flowability characteristics 3 Size of the kiln needed for manufacturing of cement is bigger 4 Raw material caWhat is the difference between the dry and wet processes
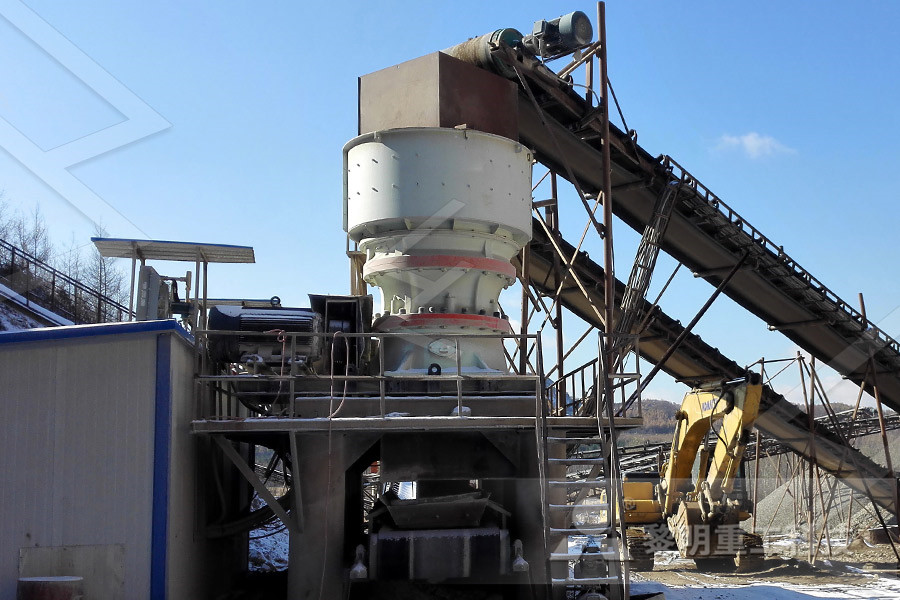
Cement Manufacturing Process: What is Cement made of
Methods of Manufacturing Process of Cement At present Portland Cement is manufactured by two processes, Dry Process, and Wet Process The main difference between these two methods of manufacturing of cement is that in the dry process, calcareous and argillaceous raw materials are fed into the burning kilns in a perfectly dry stateAt cement plant, according to different raw materials preparation methods, cement manufacturing can be divided into the dry process (including semidry process) and wet process (including semiwet process) Next, we will discuss the wet process of cement manufacturing in detailsWet Process of Cement Manufacturing Cement Wet Process Feb 25, 2018 In dry process for manufacturing of cement, the raw materials are dried and reduced in size to a fine powder in to grinding mill The dry powder is called the raw meal The raw meal is pumped into a blending silo The raw meal is blended by passinWhat is dry process in cement manufacturing? Quora
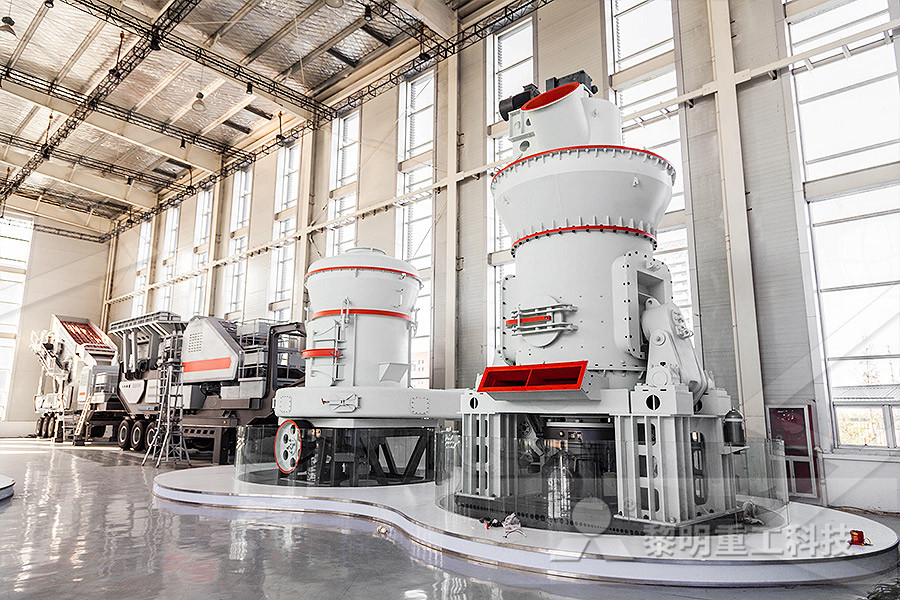
Cement Manufacturing A Wet Process with the Flow Diagram
Wet Process (The rotary kiln is an essential and important component of a cement manufacturing factory It is made of a thick steel cylinder of diameter anything from 3 meters to 8 meters, lined with refractory materials, mounted on roller bearings and capable of rotating about its axis at Dec 13, 2018 The cement manufacturing process consists of the following Steps: Grinding and mixing of the raw materials Burning of the mixture at specified temperature for a correct duration Grinding the consumed item called (clinker) along with gypsumExplain dry and wet process of cement manufacturing Jul 31, 2013 Cement manufacturing dry process Duration: 12:08 Wet Process Manufacturing Of Portland Cement Important Engineering Materials Duration: 18:57 Ekeeda 10,665 viewsCement Manufacturing YouTube
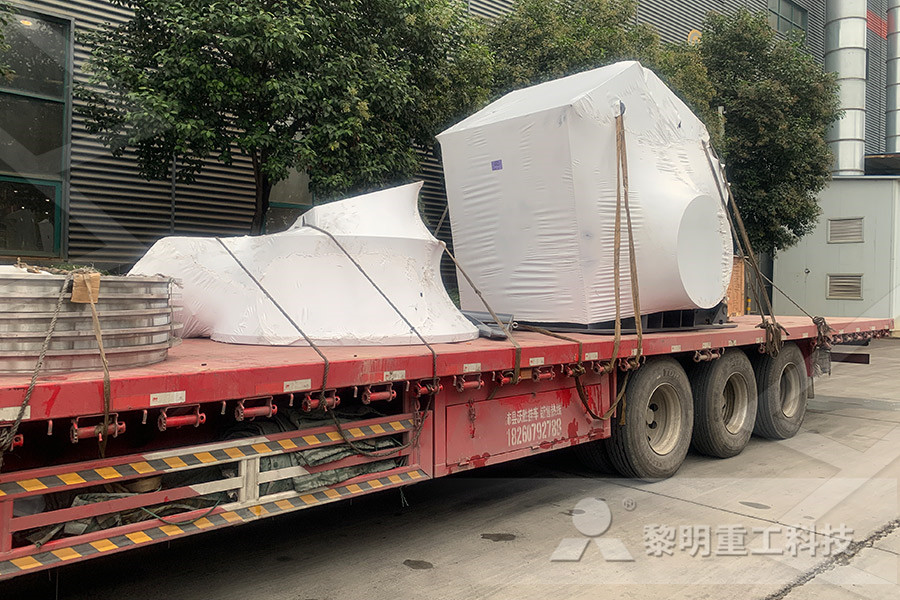
Wet process for cement manufacturing of cement by wet
Nov 27, 2019 About video:in this video we discuss the process of manufacturing of #cement by #wet method in detail Is video mein hu log cement banane ki process janenge Thanku so muchPortland cement can be made by following two different processes – a dry one and a wet one Joseph Aspdin first made portland cement in his kitchen stove in England in the 19th century Lime and silica make up approximately 85% of portland cement The materials that are commonly used are limestone, shells, chalk, shale, clay, slate, silica sand, and iron oreHow Portland Cement is Made? Manufacturing Process of Cement is so fine that 1 pound of cement contains 150 billion grains The cement is now ready for transport to readymix concrete companies to be used in a variety of construction projects Although the dry process is the most modern and popular way to manufacture cement, some kilns in the United States use a wet processHow Cement Is Made

Manufacturing the cement kiln Understanding Cement
Wet process kilns The original rotary cement kilns were called 'wet process' kilns In their basic form they were relatively simple compared with modern developments The raw meal was supplied at ambient temperature in the form of a slurry A wet process kiln may be up to 200m long and 6m in diameterMay 12, 2020 The cement manufacturing process involves several key steps, including preparing the raw materials, grinding the materials together, heating the newly formed clinker in a kiln, and finishing the cement with fine grindingSome of the main ingredients used to make cement include limestone, clay, shale, iron, and sandDifferent manufacturing techniques will use either wet or dry grinding, but What Is the Cement Manufacturing Process? (with pictures)Mar 28, 2018 Wet process Mixing of Raw materials in wash mill with 35 to 50% water Materials exiting the mill are called "slurry" and have flowability characteristics Size of the kiln needed for manufacturing of cement is bigger Raw material can be mixed easily, so a better homogeneous material can be obtained Fuel consumption is high ie,Difference between Wet and Dry process of cement – we
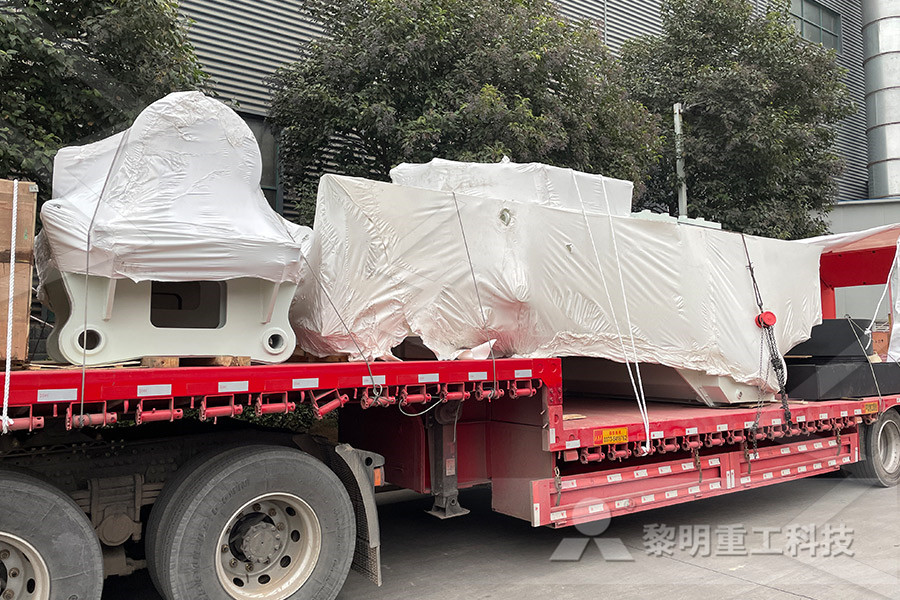
Cement Manufacturing Process Phases Flow Chart
Aug 30, 2012 Cement Manufacturing Process Phase IV: Kiln Phase Kiln is a huge rotating furnace also called as the heart of cement making process Here, raw material is heated up to 1450 ⁰C This temperature begins a chemical reaction so called decarbonation In this reaction material (like limestone) releases the carbon dioxideThe total consumption of coal in this method is only about 100 kg when compared to the requirement of about 220 kg for producing a ton of cement in the wet process The dry material undergoes a series of chemical reactions in the hottest part of the kiln and some 20 to 30 percent of the material becomes liquid, and lime, silica and alumina Dry Process for Manufacturing of Cement GharPediaMay 12, 2020 The cement manufacturing process involves several key steps, including preparing the raw materials, grinding the materials together, heating the newly formed clinker in a kiln, and finishing the cement with fine grindingSome of the main ingredients used to make cement include limestone, clay, shale, iron, and sandDifferent manufacturing techniques will use either wet or dry grinding, but What Is the Cement Manufacturing Process? (with pictures)
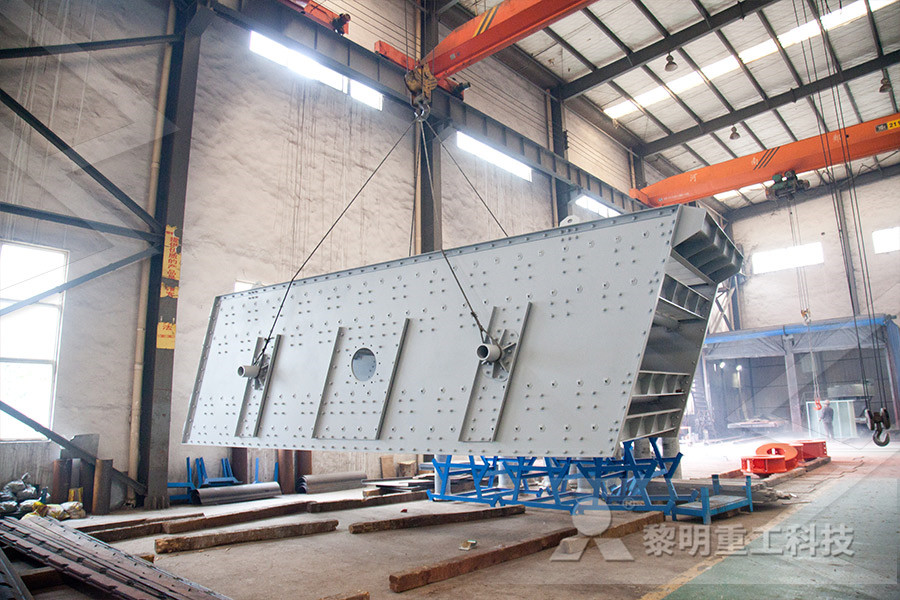
Difference between Wet and Dry process of cement – we
Mar 28, 2018 Wet process Mixing of Raw materials in wash mill with 35 to 50% water Materials exiting the mill are called "slurry" and have flowability characteristics Size of the kiln needed for manufacturing of cement is bigger Raw material can be mixed easily, so a better homogeneous material can be obtained Fuel consumption is high ie,Aug 30, 2012 Cement Manufacturing Process Phase IV: Kiln Phase Kiln is a huge rotating furnace also called as the heart of cement making process Here, raw material is heated up to 1450 ⁰C This temperature begins a chemical reaction so called decarbonation In this reaction material (like limestone) releases the carbon dioxideCement Manufacturing Process Phases Flow Chart The total consumption of coal in this method is only about 100 kg when compared to the requirement of about 220 kg for producing a ton of cement in the wet process The dry material undergoes a series of chemical reactions in the hottest part of the kiln and some 20 to 30 percent of the material becomes liquid, and lime, silica and alumina Dry Process for Manufacturing of Cement GharPedia
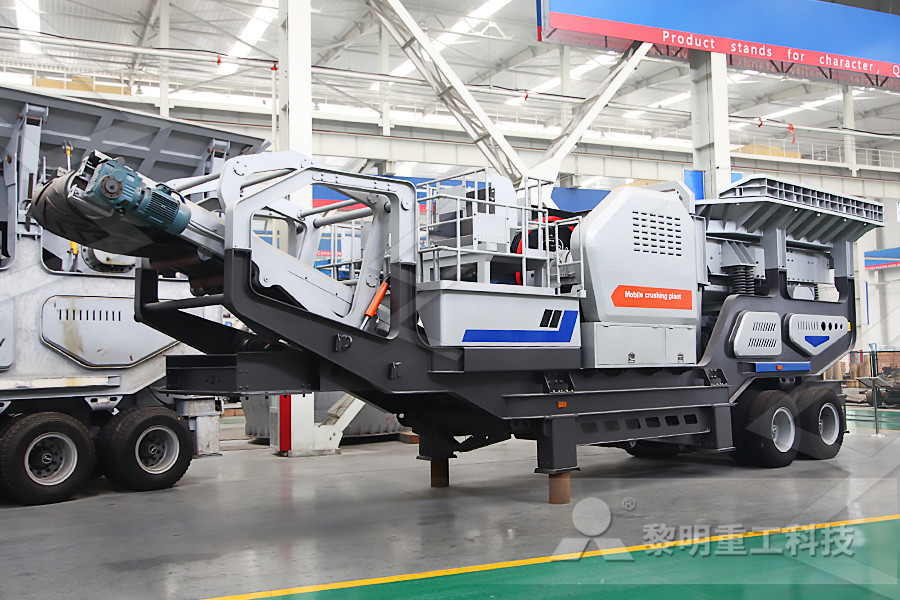
dry and wet process of cement manufacturing Mobile
Aug 10, 2015 dry and wet process of cement manufacturing Liming heavy industry is specialized in the design, manufacture and supply of crushing equipment used in mining industry The product range of our company comprises mobile crushing plant, jaw crusher, cone crusher, impact crusher, milling equipment, ball mill, vibrating feeders, screens and equipment Process Discretion: Wet process, Semidry process, Dry process and Finish process The environmental im pact of the cement production and its variations between different cement (PDF) Cement Manufacturing ResearchGateAug 27, 2015 Cement Manufacturing Process August 27, 2015 S C Rangwala Cement , Construction Material 0 The entire manufacturing process in a modern plant is now controlled through a microprocessor based programmable logic control system to maintain uniform quality of cement and a high rate of productionCement Manufacturing Process Civil Engineering Blog
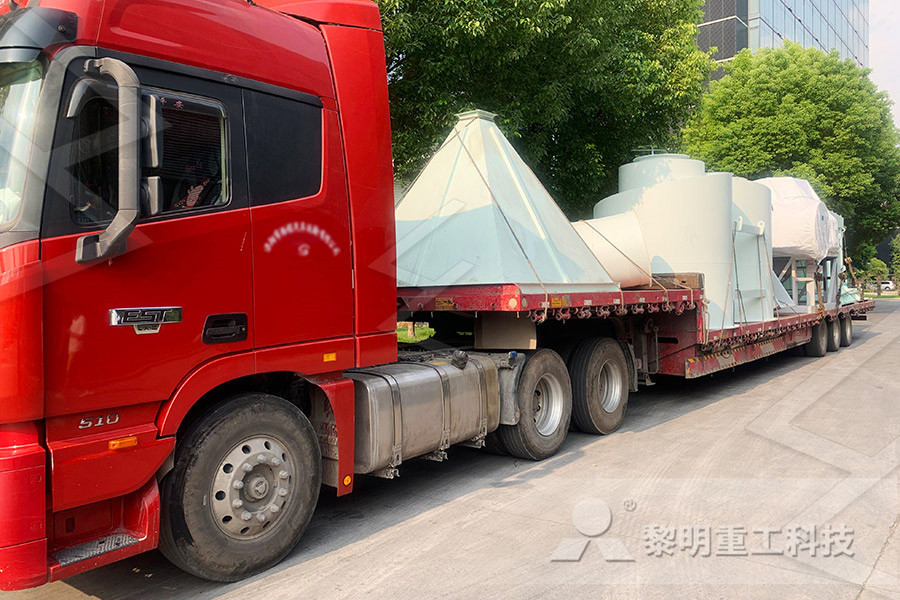
116 Portland Cement Manufacturing
Portland cement manufacturing plants are part of hydraulic cement manufacturing, which also includes natural, masonry, and pozzolanic cement The sixdigit Source Classification Code (SCC) for portland cement plants with wet process kilns is 305006, and the sixdigit SCC for plants with dry process kilns is 305007 Portland cement accounts In process engineering Wet process may refer to: Wet sulfuric acid process for the manufacture of Sulphuric acid; Any wet process in textile engineering, see Wet processing engineering; The wet process in Coffee production; The wet process in Coconut oil production; The wet process used in cement manufacture in Cement kilns; A wet process in the manufacture of Separators for Wet process WikipediaThe cement industry has boosted efficiency by concentrating new capital investment in plants that use the dry process of cement manufacture, and by phasing out operations that rely on the more energyintensive wet process Since 1974, the number of wet process kilns has dropped from 234 to 25 a decline of 89 percent while the number of Cement Industry Overview Portland Cement Association
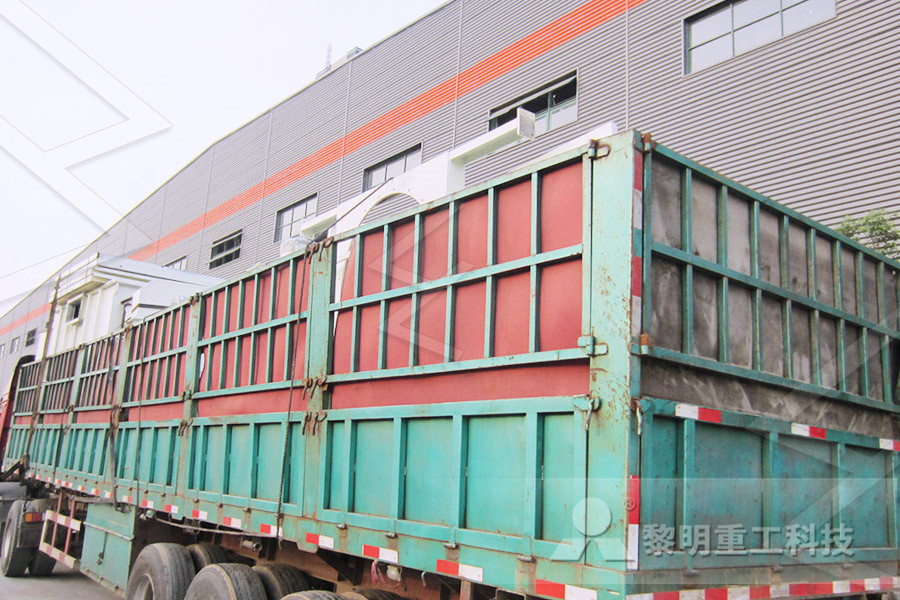
Energy and Cost Analysis of Cement Production Using the
The study evaluates the energy consumption of both wet and dry processes cement manufacturing plant in Nigeria Enrgy consumption data collected for the period 2003 to 2011 were used to estimate the energy consumption of the crushing, milling, agitation, burning, grinding and bagging operations The total energy evaluation was based on the three primary energy sources which include electrical Cement grinding As the last process, the cement grinding will consume a great deal of electricity And in this process, special size granule cement will be obtained (7) Cement Packaging The cement can be transported in bulk or in bags 2Wet cement process The manufacture of cement is a very carefully regulated process comprising the Cement making process Great Wall CorporationCement Cement Extraction and processing: Raw materials employed in the manufacture of cement are extracted by quarrying in the case of hard rocks such as limestones, slates, and some shales, with the aid of blasting when necessary Some deposits are mined by underground methods Softer rocks such as chalk and clay can be dug directly by excavatorsCement Extraction and processing Britannica
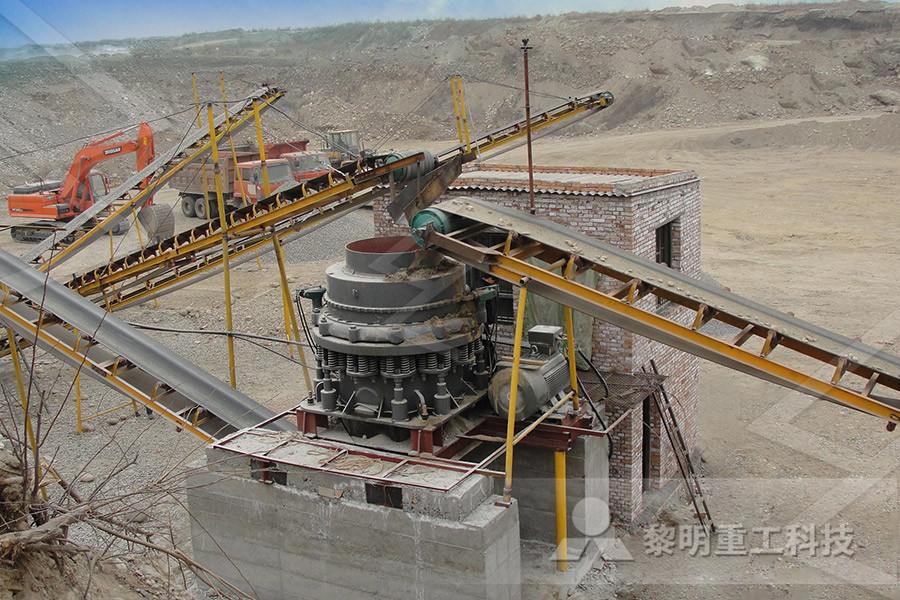
Manufacturing of cement LinkedIn SlideShare
Jan 10, 2018 Manufacturing of cement By DRY process 13 WET Process • The raw materials are firstly crushed and made into powdered form and stored in silos The clay is then washed in washing mills to remove adhering organic matters found in clayThe study evaluates the energy consumption of both wet and dry processes cement manufacturing plant in Nigeria Enrgy consumption data collected for the period 2003 to 2011 were used to estimate Energy and Cost Analysis of Cement Production Using the Cement grinding As the last process, the cement grinding will consume a great deal of electricity And in this process, special size granule cement will be obtained (7) Cement Packaging The cement can be transported in bulk or in bags 2Wet cement process The manufacture of cement is a very carefully regulated process Cement making process Great Wall Corporation

Dry process of cement – we civil engineers
Aug 24, 2018 Dry process These are two different processes of manufacturing cement wet process minerals are wet ground (by adding water) to form a slurry and then dried, dry process minerals are dry ground to form a powder like substanceBoth the processes are in use and have their own advantages and disadvantagesWhile in wet process grinding is easier,in dry process Cement Cement Extraction and processing: Raw materials employed in the manufacture of cement are extracted by quarrying in the case of hard rocks such as limestones, slates, and some shales, with Cement Extraction and processing BritannicaJan 10, 2018 Manufacturing of cement By DRY process 13 WET Process • The raw materials are firstly crushed and made into powdered form and stored in silos The clay is then washed in washing Manufacturing of cement LinkedIn SlideShare
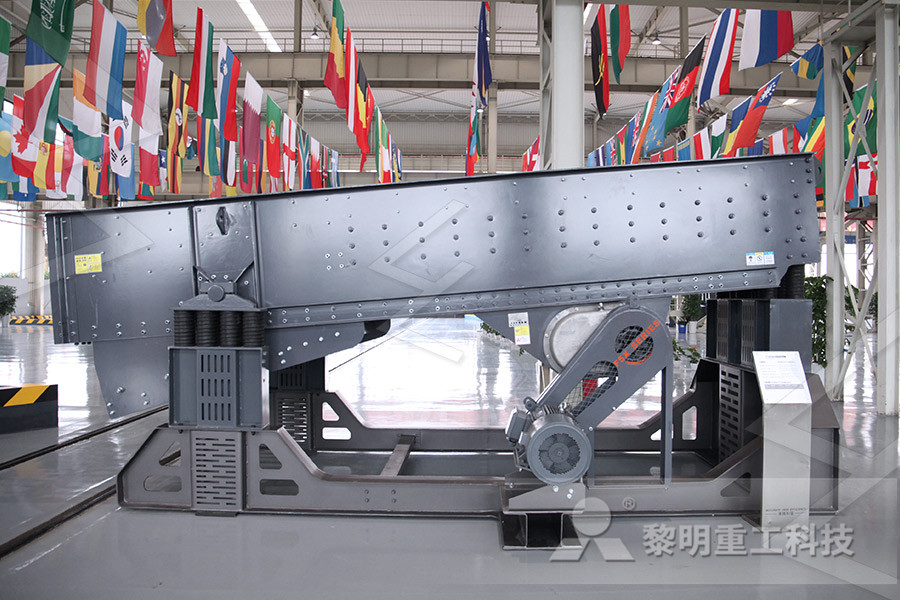
The Manufacture of Portland Cement
The steps involved here depend on the process used There are two main cement manufacturing processes currently used in New Zealand: the dry process (used by Golden Bay) and the wet process (used by Milburn) The dry process uses more energy in grinding but less in the kiln, and the wet process has lower overheads than the dry processThe production of cement is either through the wet or dry process with the dry process as the preferred option because of the lower energy intensity Cement production accounts for about 5% of Cement Production an overview ScienceDirect Topics• Chalk is porous and often has high moisture content that leads it to its use in the ‘semidry/wet’ manufacturing process of making cement This particular process represents some 16% of total productionCement: Materials and manufacturing process
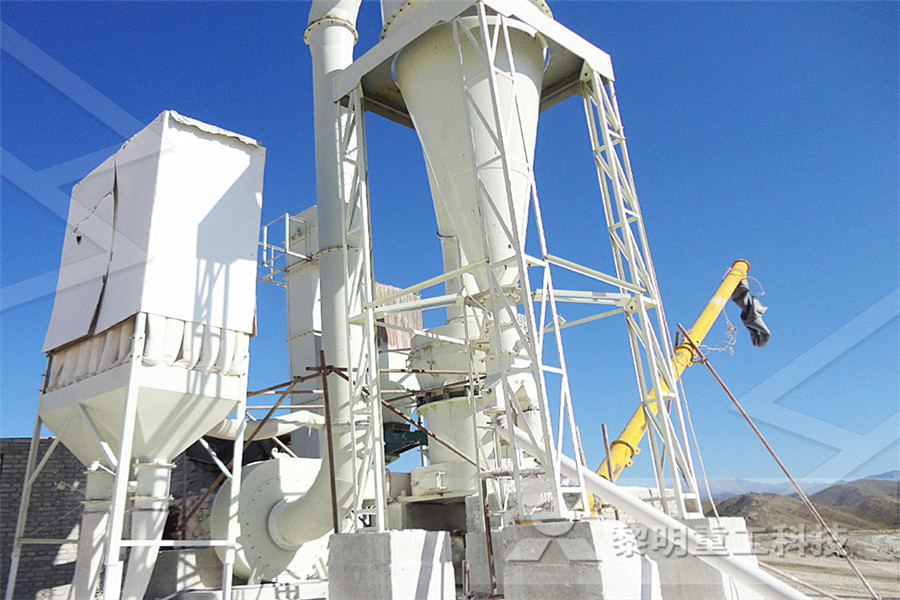
Manufacture of Portland cement University of Technology
Methods of cement manufacturing 1 Wet process grinding and mixing of the raw materials in the existence of water 2 Dry process grinding and mixing of the raw materials in their dry state The process Portland cement and process of Manufacturing what is Portland Cement Portland cement is an extreme ground material having adhesive and cohesive properties, which provide a binding medium for discrete ingredients It is hydraulic cement What is Portland cement and process of Manufacturing, Dry Aug 15, 2017 The Cement Manufacturing Process Cement is a finely ground powder which, when mixed with water, forms a hardening paste of calcium silicate hydrates and calcium aluminate hydrates Cement is used in mortar (to bind together bricks or stones) and concrete (bulk rocklike building material made from cementThe Cement Manufacturing Process Process Systems
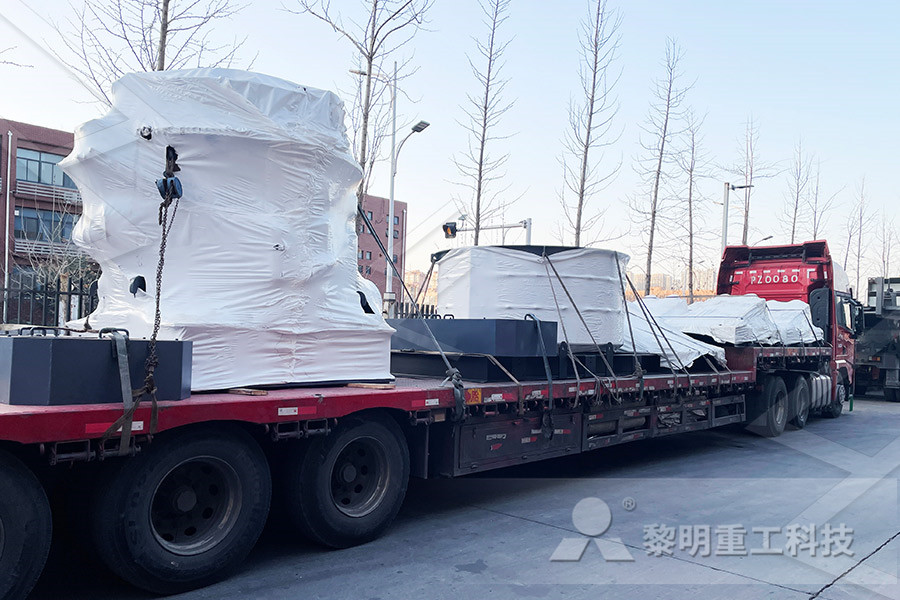
CEMENT MANUFACTURING PROCESS AND ITS SELECTION: WET
This process was especially evolved to counter the main drawback of the wet process ie high fuel consumption In this process, the raw materials ground in dry condition are homogenized and then Mar 21, 2018 Concrete Manufacturing Process consists of many stages The Concrete mix for delivery from a plant instead of mixing on the job site The concrete mixes, transports and delivers to a construction site to place in formworks for construction And to form various structures, like a column, beam, slab, etc Concrete Manufacturing ProcessConcrete Manufacturing Process in modern constructionJan 28, 2017 Cement is topic;like and give credit for my free work cement cement and its types Manufacturing of cement uses of cement wet process dry process portland ce Slideshare uses types and manufacturing of cement LinkedIn SlideShare